Sappi Fine Paper North America
Maker of coated papers for web and offset printing
Maker of release papers for surface impressions on synthetic materials
Since the first paper made from wood pulp originated in China in 1 A.D., what was once considered an art has evolved into a science, and more recently, forensic science.
“Pretty much every piece of analytical instrumentation they have on CSI, we have here at Sappi,” says Dr. Jon-Marc (JM) Rodier, Manager of Analytical, Print Test and Safety, referring to the popular television program with its focus on forensics. Instead of looking at gunpowder, blood, or fingerprints, however, Rodier and the Sappi team analyze the fibers and coatings of many different grades, shades, and weights of papers designed for a variety of printing requirements. They assist with resolving production issues in the manufacturing and printing process by identifying sources of contamination or causes of quality defects. Not only do they help with the development of new products for web and offset printing, as well as release papers used to imprint texture on synthetic vinyls and other materials, they identify sources of customer issues from outside contamination to changes in operation parameters and incompatibility in the customers’ raw materials.
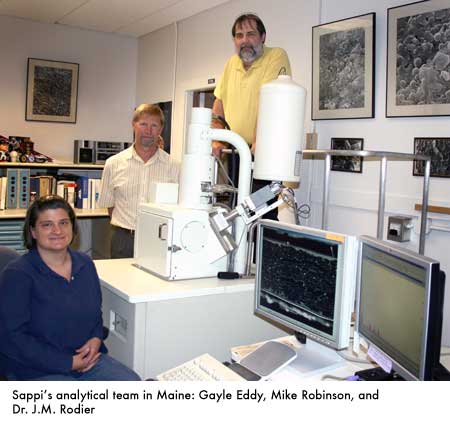
One of North America’s leading papermaking companies, Sappi Fine Paper North America produces 1.3 million tons of coated fine, specialty, and technical papers a year. Even though the company’s first coated and “calendered” paper was produced in 1881, the process of developing new papers, grade line extensions, and processes to improve the printing quality of papers used in magazines, brochures, and product packaging is never-ending, and they closely track the quality from pulp to printed product.
Sappi’s Technology Center is located in Westbrook, Maine just north of Portland, across from the site of the first paper making facility in the United States, established in 1854 under the name of S.D. Warren Company. A 1920s paper machine still operates in the papermaking plant, upgraded of course to keep pace with the other more modern machines used by Sappi worldwide. All are turning pulp into paper, after converting a 95% water-based mixture into a material that will be calendered, a process that applies temperature and pressure to exact specifications. The paper is trimmed and sold to printers where it is run on a printing press where it must exhibit specific characteristics in its ability to accept a variety of inks and produce images that pop off the page.
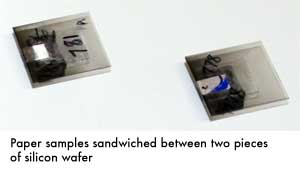
The Technology Center is where the analytical department operates the more scientific instrumentation, including two newer model scanning electron microscopes and two cross section polishers, or sample preparation equipment, that co-exist in environmentally-controlled labs. When looking at paper samples, the analytical team relies on their working knowledge of the mill’s big paper machines and their characteristics, familiarity with carefully guarded paper recipes and their fingerprints, and their knowledge of chemistry as well as microscopy. It all comes into play when they look at a cross section of paper in the electron microscope and can see exactly what is inside the space between the two coated sides.
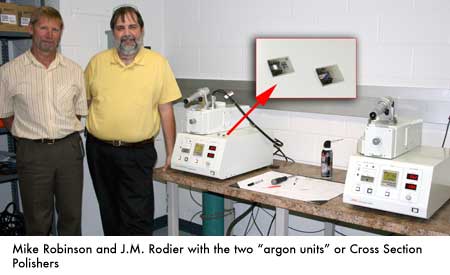
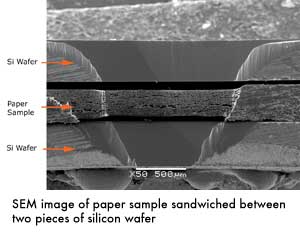
The term “paper thin” takes on a whole new meaning when you are trying to look inside the very edge of the paper (the razor-sharp culprit for those office paper cuts) and see what’s happening in there. Think of a sheet of paper as an ultrathin sandwich with 1 micron of ink on top of 10 microns of paper coating, which covers approximately 40-200 microns of fiber in the middle (depending upon the grade of paper). Now think of cutting that ultrathin sandwich so that you could look at it on edge without any distortion – a perfect slice that is neither squished nor smeared. You want to see the uniformity of the coating over the fibers. You want to see the fiber matrix and look for defects such as holes and debris. You want to see how the ink adheres to the paper – whether it’s sitting on top if it, or if it has been absorbed into the coating. You want to see these things, but can you really see them clearly?
This type of pristine cross section of a material with characteristics like paper wasn’t possible two or three years ago. A common technique such as freeze fracture was typically employed. Rodier, who has been at the paper company for nearly 15 years, says he routinely used the freeze fracture technique to help him prepare the paper sample and examine it on edge in the electron microscope. Rapid freezing with liquid nitrogen, followed by cutting the paper with a razor blade, produced a sharp edge, as did microtomy, which cuts the sample automatically with a rotary blade, but neither technique produced a clean cross section – there was always distortion and smearing.
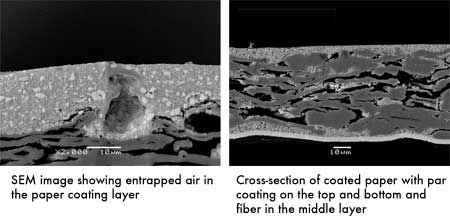
To make matters worse, using microtomy physically altered the sample. “The sample was embedded in epoxy but the resin penetrated the sample and because organic materials have the same contrast it was hard to differentiate between the paper and the resin,” says Mike Robinson, who performs the analytical microscopy work. Mike started working at the Westbrook paper mill 26 years ago, on the paper machines like his father who also worked at the mill. He eventually transferred to the graphic arts department, then learned fiber microscopy at McCrone, Lehigh, and JEOL when he became increasingly involved in the analytical process.
When Rodier and Robinson learned of a new product from JEOL that cuts samples with an argon beam and produces a pristine cross section, they asked to see if it would work on paper without melting it. The resulting images revealed crisp details. They worked with Dr. Natasha Erdman at JEOL to develop a way of preparing the sample by sandwiching it between two glass slides that act as a heat sink. Now two JEOL cross section polishers, which they call Argon Units, run side-by-side around the clock producing samples to be imaged with the two electron microscopes in Sappi’s lab.
It’s no oxymoron that modern paper making technology, while it seems to be an old industry, is using state-of-the-art techniques and always improving the quality of its products. “We lead the technology in paper making – the way it’s finished, whether it’s dull, matte, or gloss – the consistency from lot to lot,” said Rodier. S.D. Warren Company owned the first SEM in the state of Maine, more than 30 years ago, and added another later. Both are retired and replaced by Sappi with two newer SEMs. “We have much tighter tolerances now,” said Rodier.
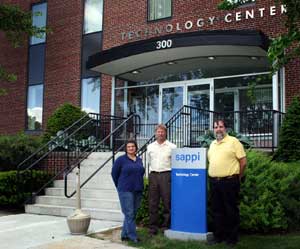
In recent years, the Sappi team has increased its analytical capability focusing not only on new instruments but new and innovative methods, including sample preparation, which is what the cross section polishers do. “We had a forensics student work here once as a co-op and she helped us improve our sample collecting procedures. Sample prep is the biggest thing - if it’s not in the right condition it limits what you can do. Our analytical support is unique in the paper industry,” said Rodier.
Sappi Limited is a global company that was founded in 1936, and acquired S.D. Warren in 1994. “We are a leading producer of coated fine paper in a world where, despite many predictions to the contrary, paper and print continue to play a more important role in our daily lives than ever before,” their history states. While what’s on the paper may be most important to the majority of us, what’s in the paper is clearly seen now at Sappi where cutting the paper with an argon beam, instead of a blade, is just one more process that aids their investigations.